
TARCZA PRZEWORSKA (II-III vne)
Opisana tutaj rekonstrukcja tarczy
,,Przeworskiej" została wykonana w 1999r. na zlecenie ,, ŚWIĘTOKRZYSKIEGO STOWARZYSZENIA
DZIEDZICTWA PRZEMYSŁOWEGO "
na podstawie duńskich wykopalisk bagiennych, oraz materiałów ze zbiorów
,, Państwowego Muzeum Archeologicznego w Warszawie " i ,, Muzeum Starożytnego
Hutnictwa Mazowieckiego w Pruszkowie ".
|
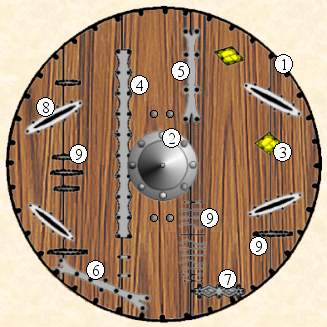 | |
Najprawdopodobniej
nigdzie na świecie nie dotrwała do naszych czasów żadna kompletna tarcza z tego okresu.
Wszystko, co wiemy o ich wyglądzie i konstrukcji, to tylko mniej lub bardziej śmiałe przypuszczenia wysnute na
podstawie ozdób w formie miniaturki tarczy, resztek okuć pozostałych po przepaleniu w stosie pogrzebowym,
czy nielicznych zachowanych fragmentów desek z okuciami (Dania).
Średnica tarczy wyliczona na podstawie udostępnionych mi fragmentów okuć
rurkowatych waha się od 50 do 150 cm. Ta znaczna rozbieżność wyników da
się wytłumaczyć, jeśli przyjmiemy założenie, że tarcza mogła mieć kształt
owalny, lub nastąpiło odkształcenie badanych okuć pod wpływem wysokiej
temperatury stosu pogrzebowego. Zgadza się to z wymiarami zachowanych
fragmentów tarcz (Thorsberg). Płyta tarczy została sklejona z desek
olchowych o gr. 14 mm, zestruganych następnie do 4 mm. (przy krawędzi).
Aby maksymalnie ograniczyć deformacje drewna pod wpływem zmian
wilgotności, zastosowałem deski cięte przez rdzeń (ze środka przekroju
pnia), sezonowane przez 5 lat. Okucia przybijane do powierzchni tarczy nie
miały na celu tylko łączenia poszczególnych desek ze sobą [4;5;6;8;9].
Świadczą o tym zachowane jednolite (bez pęknięć i podziałów) fragmenty
desek z przynitowanymi do nich okuciami [7]. Możliwe też, że całą tarczę
wykonywano tylko z dwóch szerokich desek, a nawet jednej. W tym przypadku
pozornie przypadkowe, bez związku z podziałem desek rozmieszczenie
niektórych okuć na powierzchni tarczy zaczyna mieć sens. Małe okucia,
często wykonane z brązu [3], nie miały raczej znaczenia konstrukcyjnego i
moim zdaniem były elementami przede wszystkim dekoracyjnymi. Okucia
długie, posiadające z reguły szereg otworów umieszczonych wzdłuż krawędzi
[4;5] najczęściej wiązały ze sobą dwie przylegające do siebie deski, ale
mogły też wzmacniać miejsce osłabione, grożące pęknięciem ,,po słoju".
Osobną kwestią jest ich znaczenie jako elementów zwiększających odporność
tarczy na ciosy bronią. Z pewnością wszystkie te okucia wzmacniały
konstrukcję samej płyty, choć i tak wydaje się ona zaskakująco delikatna.
Jednak podstawowym okuciem wiążącym ze sobą poszczególne deski lub
chroniącym krawędź tarczy przed pękaniem (w pewnym stopniu i przed ciosem
miecza) mogło być tylko okucie krawędzi[1] (okucie
rurkowate).
OKUCIE RURKOWATE [1]
Niemożliwe niestety było zbadanie z ilu części
się ono składało i jak je ze sobą łączono. Wykonanie jednolitej obręczy o
obwodzie prawie 3 metrów, choć konstrukcyjnie najlepsze, byłoby bardzo
skomplikowane, a więc raczej mało prawdopodobne. O wiele łatwiej wykuć
paski blachy mniejszej długości i dlatego przyjąłem, że ze względów
technologicznych najwygodniej jest podzielić obwód tarczy na 4 odcinki, co
daje długość pojedynczego paska około 60 cm. Oczywiście nie miałem do
dyspozycji łupki żelaznej, a więc odtworzenie całego procesu kucia było
nierealne. Mogłem rozpocząć pracę dopiero od etapu gotowej sztabki żelaza.
Do wykonania takiego fragmentu okucia wystarczy pręt o przekroju
1×1 cm i długości 25 cm (ok. 150& ÷ 200 g. żelaza). Przekucie takiego pręta na
wymagany pasek blachy jest stosunkowo proste i nie wymaga wielokrotnego
rozgrzewania, co przy stosunkowo dużej powierzchni prowadziłoby do
znacznych ubytków materiału z powodu jego utleniania. Przy użyciu młotków
o masie 0.5 ÷ 0.8 kg. i kowadełka o masie 6 kg. zajęło mi to
ok. 20 minut. Nadanie tak uzyskanemu paskowi ostatecznego kształtu
(wycięcie półkolistych uszek pod nity) za pomocą przecinaka, przebicie
otworków a w końcu opiłowanie wymaga ok. 2 godzin. Tyle samo czasu zajmuje
zwinięcie go w rurkę i dopasowanie jej do krzywizny krawędzi tarczy.
Osobną sprawą jest wykonanie nitów. Mając do dyspozycji przygotowany
wcześniej pręt o odpowiednim przekroju, można wykuć 40 nitów w ciągu
4 ÷ 5 godzin. Jak więc widać, samo wykonanie
wszystkich elementów okuć krawędzi tarczy zajęło mi ok. 25 godzin. Z
pewnością starożytny kowal miał bez porównania większą niż ja wprawę i
wiedzę w tym zakresie, na pewno nie pracował sam, ale musiał też wykonywać
półfabrykaty, których ja robić już nie potrzebowałem. Przypuszczam, że
całkowity czas, jaki był konieczny do wykonania i zamocowania takiego
okucia to trzy ÷ cztery dni.
UMBO[2]
Umbo, a zwłaszcza umbo z kolcem jest bez wątpienia najbardziej skomplikowanym technologicznie elementem w całej
tarczy. Wydaje się to nieprawdopodobne, ale wykonanie rekonstrukcji
technologicznej umba jest trudniejsze niż wykucie przeciętnego miecza!.
Nie mówię tutaj o majstersztyku sztuki kowalskiej - rzymskim mieczu
dziwerowanym(1), ale wykucie tak skomplikowanego kształtu z
jednego kawałka żelaza, i to bez spawania, było też sztuką samą w sobie. Nie mogę stwierdzić z
całą pewnością, czy formą wyjściową był krążek blachy, czy okrągła płytka
(bryłka) o większej grubości. Jeden i drugi sposób kucia jest możliwy i o
podobnym poziomie trudności. Przypuszczam, że jednoznacznej odpowiedzi
mogłyby nawet nie dać specjalistyczne badania zachowanego materiału
archeologicznego. Cały problem sprowadza się do tego, czy formę ostateczną
uzyskiwano poprzez rozkuwanie (,,wytłaczanie") materiału, czy odwrotnie -
spęczanie. Dla laika jest to w zasadzie bez znaczenia - ostateczny efekt
jest przecież taki sam. Być może kuto umba na oba sposoby, a wybór
konkretnego mógł zależeć od mody, tradycji danego ośrodka kowalskiego czy
choćby indywidualnego wyboru kowala. Na pewno umba bez kolca lub z kolcem
krótkim, guziczkowatym, kuto łącząc obydwie metody. Umbo z długim kolcem
(takie jak w opisywanej tarczy) wykute z blachy ma kolec wewnątrz ,,pusty",
a wykute z bryłki (wytłaczanie) miałoby kolec pełny. Specjalnie napisałem
,,pusty", gdyż owa ,,pusta przestrzeń" może być tylko miejscem styku zakutej
blachy (podobnie jak ,,przestrzeń" we wnętrzu zaciśniętej pięści). Nie
zawsze da się to zaobserwować ,,na oko", gdyż przy nasadzie kolca jedna i
druga forma może wyglądać identycznie, nawet na kolcu uszkodzonym. Różnice
te można by jednoznacznie zaobserwować dopiero na szlifach, ewentualnie na
zdjęciach RTG. Nie słyszałem jednak, aby prowadzone były badania pod tym
kątem.
|
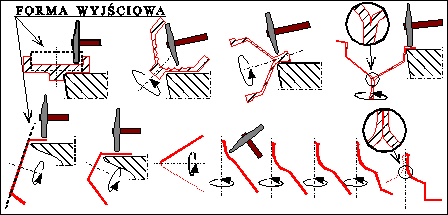 | |
Na rysunkach podałem tylko kształt i wymiary
zewnętrzne, natomiast grubość ścianek typowego umba waha się w granicach
0,8 ÷ 1,5 mm. i jest prawie identyczna na całym obwodzie danego
egzemplarza (w większości przypadków w granicach kilku dziesiątych mm).
Uzyskanie tak równej ścianki jest znacznie łatwiejsze w przypadku kucia z
krążka blachy, jednak w tej metodzie niezbędne jest kowadło o walcowatym
kształcie, a więc bardzo wyspecjalizowane, potrzebne w zasadzie wyłącznie
do kucia umba. Przyjmując jako formę wyjściową spłaszczony walec, do całej
pracy wystarczy tylko jedno, typowe kowadełko o płaskiej powierzchni
roboczej. Jedna i druga metoda jest bardzo pracochłonna, wymagająca
wielokrotnego rozgrzewania metalu. Rozwinięta powierzchnia powoduje bardzo
szybkie stygnięcie, pozwalając niekiedy na dosłownie kilkanaście uderzeń
młotkiem. Nie wdając się w szczegóły poszczególnych operacji, można
przyjąć czas wykonania kompletnego umba nawet na dwa dni.
OKUCIE TAŚMOWATE PODŁUŻNE [4;5]
Nie chcę tworzyć tutaj jakiegoś prywatnego
nazewnictwa, jednak skoro opisuję różne typy okuć, to muszę je jakoś
nazwać. Uważam, że okucie nazwane przeze mnie ,,podłużnym'', wiązało
sąsiednie deski wzdłuż ich krawędzi. Świadczą o tym nity ustawione parami
i brak nitów pojedynczych, które przy tego rodzaju połączeniu musiałyby
przechodzić w miejscu styku łączonych desek, a więc zupełnie bez
sensu.
|
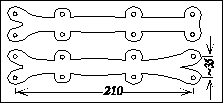 | |
Różnorodność form takich okuć jest duża, ja
zastosowałem tutaj tylko dwie. Na górze rysunków przedstawiłem okucie
wewnętrzne, poniżej odpowiadające mu okucie umieszczone po zewnętrznej
stronie tarczy. Okucia tego typu wykuwano z blachy o gr. 1 ÷ 1,5 mm. Ich
krawędzie często zdobiono ornamentem punktowanym, lub (jak na pierwszym
rysunku) wypukłym ornamentem perełkowanym. Kształt tych okuć jest bardzo
podobny do okucia rurkowatego, podobna jest też i ich pracochłonność -
wykonanie obydwu okuć zajęło mi ok. 15 godzin, (10-okucia, 5-nity)
OKUCIE TAŚMOWATE POPRZECZNE [6;7]
Okucia tego typu nie mogły biec wzdłuż linii łączenia desek ani wzdłuż słojów, gdyż pojedyncze, ustawione w szeregu
nity nie tylko by nie wzmacniały, a wręcz osłabiały deski. Jedynym
logicznym ich położeniem jest układ w poprzek słojów lub po skosie. Okucie
górne zdobione jest wybijanym ornamentem liniowym i perełkowym.
Na rysunku przedstawiłem tylko okucia
zewnętrzne. Konstrukcyjnie okucia te niczym się nie różnią od okuć
opisywanych powyżej.
OKUCIE POPRZECZNE Z ŻEBERKIEM. [8]
Okucie to, z racji biegnącego wzdłuż
przetłoczenia (żeberka) prawdopodobnie usztywniało płytę tarczy w miejscu
najbardziej narażonym na zwichrowania, a więc w pobliżu krawędzi. Deski w
tym miejscu mają grubość ok. 4 ÷ 5 mm, a więc ich sztywność w poprzek
słojów jest znikoma i dlatego łatwo wyginają się pod wpływem zmian
wilgotności. Nałożenie na tak osłabione miejsce podobnego okucia zupełnie
zapobiega takim odkształceniom. Oparte jest to na konkretnym
doświadczeniu. Z kilku wykonanych przeze mnie tarcz, tarcza z opisanymi
tutaj okuciami była bez porównania sztywniejsza od tarczy z okuciami bez
żeberek i nie wichrowała się w tym miejscu.
Górna część rysunku przedstawia okucie
wewnętrznej strony tarczy, dolna zewnętrznej.
KLAMRY. [9]
Są to typowe
okucia łączące dwie sąsiednie deski, lub wzmacniające deską pękniętą.
Występują w bardzo zróżnicowanej formie, począwszy od prostych klamerek z
wygiętego drutu żelaznego, po starannie odkute i zdobione klamry
brązowe.Przybijane były zarówno pojedynczo, jak i szeregiem
po kilka - kilkanaście w jednej grupie. Są to bardzo proste w wykonaniu
okucia. W większości przypadków wykonanie i zamocowanie jednej klamerki
zabiera kilkanaście minut do pół godziny. Pokazane na rysunkach klamry,
zdobione są szeregiem rowków naciętych półokrągłym pilnikiem lub piłką -
szczegóły wyjaśniają rysunki obok.
IMACZ
Imacz wraz
z umbem tworzy jakby centralny węzeł wiążący deski ze sobą, będąc
jednocześnie punktem uchwytu tarczy w jej najsilniejszej, dodatkowo
opancerzonej umbem części. Nie spotkałem się z opisem rzemieni czy śladów
ich ewentualnego mocowania do desek tarczy, a więc imacz był
najprawdopodobniej jedynym uchwytem, za który tego typu tarczę trzymano.
Jednocześnie wiadomo, że masywniejsze tarcze legionistów rzymskich
posiadały oprócz imacza rzemienną pętlę, przez którą przekładano ramię, a
więc tarczę trzymano stosunkowo blisko ciała - na odległość przedramienia.
Opisywana zaś tutaj tarcza, mogła być trzymana nawet na odległość
wyciągniętej ręki. Być może to właśnie tłumaczy jej delikatną budowę.
Stosunkowo lekka i niewielka tarcza, trzymania w ugiętej, amortyzującej
tym samym siłę ciosu ręce, pozwalała na znaczną mobilność a więc i na
zastosowanie lżejszej konstrukcji.Technologicznie jest to
nieco bardziej skomplikowane okucie od poprzednio opisanych, ale i jego
wykonanie nie mogło stanowić dla przeciętnego kowala problemu.
Przypuszczam, że wykuwano najpierw pasek blachy o grubości 1÷2 mm.
następnie wycinano z grubsza kształt przyszłego imacza i zaginano całość w
kształt rynienki. Teraz należało rozpłaszczyć końce, jednocześnie
wytłaczając ,,garb'' w miejscu przejścia płaskich zakończeń imacza w jego
rynienkowaty uchwyt. Cały proces kucia przebiega z użyciem tylko jednego
typowego młotka, kując jego obuchem (część płaska) lub rombem (część
wąska). Jako miękkie kowadło do kucia wklęsłych fragmentów stosowano
prawdopodobnie drewno. Na postawionym pionowo pieńku z twardego drewna
(dębina, olcha) można z powodzeniem tłoczyć blachę nawet na gorąco. Przy
zastosowaniu takiego pieńka i wymienionego poprzednio kowadełka, do
wykucia i opiłowania imacza wystarcza 4 ÷5 godzin.
Imacz zamocowany był w
poprzek wyciętego po środku tarczy otworu, zasłoniętego od zewnątrz umbem.
Wewnątrz imacza umieszczano drewniany rdzeń, którego wpuszczone w płytę
tarczy końce przynitowane były dwoma przeciwległymi nitami mocującymi
jednocześnie umbo.
W zasadzie w tym momencie można już mówić o gotowej
tarczy, choć być może deski malowano i nasączano na gorąco olejem czy
woskiem. Z pewnością woskowanie chroniło w znacznym stopniu drewno tarczy
przed wilgocią, więc prawdopodobnie je stosowano, ale tego jednoznacznie
potwierdzić się nie da. Malowanie jest właściwie tylko zabiegiem
kosmetycznym, ale jeśli wziąć pod uwagę znaczny koszt takiej tarczy, to
chęć dodatkowego ozdobienia tak cennego przedmiotu jest chyba naturalna.
Oczywiście świadomie pomijam kultowe czy magiczne przesłanki malowania
tarczy.
Określiłem tutaj tarczę jako bardzo
cenny przedmiot. Uważam, że była ona chyba najdroższym elementem
wyposażenia ówczesnego wojownika, a przynajmniej najbardziej
pracochłonnym. Trudno przypuszczać, aby ,,barbarzyńskie'' tarcze, podobnie
jak i inne elementy uzbrojenia, produkowały warsztaty rzymskie na potrzeby
swoich przeciwników militarnych, tym samym uzbrojenie to, a przynajmniej
znaczna jego część musiała być wytwarzana na terenach ,,Barbaricum''.
Oczywiście handel bronią istniał tak dawno, jak dawno człowiek tę broń
wytwarzał, a więc i rzymska broń trafiała na nasze tereny. Jej cena nie
była z pewnością porównywalna do ceny wytworów rodzimego ,,przemysłu
zbrojeniowego''. Większość archeologów zakłada, że ,,Barbaricum'' nie
potrafiło produkować mieczy ,,dziwerowanych", a każdy egzemplarz takiego
miecza musi być rzymskim importem. Osobiście nie zgadzam się z tym, ale
jeśli było tak naprawdę, to tarcza pod względem pracochłonności nie miała
wśród miejscowych wyrobów żadnej konkurencji. Jeśli przyjmiemy, że
starożytny kowal musiał poświęcić na wykucie i zamontowanie wszystkich
elementów tarczy tyle samo czasu co ja, to otrzymamy:
|
DETAL + NITY |
ŁĄCZNY CZAS [godziny] |
|
WYKUCIA |
MONTAŻU |
|
Okucia rurkowate (komplet) |
25 | 12 |
|
Umbo | 20 | 5 |
|
Okucia taśmowate |
15 |
5 |
|
Okucia z żeberkiem |
10 |
2 |
|
Klamry |
6 |
2 |
|
Imacz |
5 |
5 |
|
Deski - ostruganie, spasowanie itp. |
12 |
|
Wykończenie |
5 |
|
RAZEM |
129 |
|
Otrzymana liczba ~130
godzin jest może szokująca, ale jeśli przyjmiemy, że została ona zawyżona
nawet o 30%, to i tak otrzymamy blisko dwa tygodnie pracy nad jedną
tarczą. Do tego trzeba jeszcze dodać czas potrzebny do uzyskania samego
żelaza i wykucia z niego wyjściowych sztabek, czego nie podejmuję się
oszacować.
W tym miejscu nasuwa się
pytanie, czy taką tarczę mógł wykonać jeden kowal, czy było ich kilku. Na
podstawie jakości detali, (zwłaszcza umba) a właściwie wprawy w ich
wykonywaniu mogę przypuszczać, że nie mógł tego wykonać przeciętny
,,wiejski'' kowal. Regularność kształtu, a przede wszystkim bardzo trudna do
uzyskania jednakowa grubość ścianek da się pogodzić tylko z dużą wprawą
wynikającą z wykonania wielu takich samych przedmiotów. Nawet bardzo
doświadczony kowal musi wykuć najpierw kilka nieudanych egzemplarzy, zanim
nauczy się wszystkich niuansów technologicznych. Zaryzykowałbym w tym
miejscu stwierdzenie, że przynajmniej w ogromnej większości przypadków
tarcza nie była pojedynczym, sporadycznym wyrobem miejscowego kowala, ale
musiała być dziełem grupki kilku osób wykonujących wspólnie wiele
podobnych tarcz. Nie wiem, jak to stwierdzenie ma się do rzeczywistości,
ale nie mogę sobie po prostu wyobrazić pojedynczego kowala pracującego na
potrzeby swoich sąsiadów, mogącego pozwolić sobie na długotrwałe i
kosztowne eksperymenty tylko po to, aby zrobić kilka kiepskich
tarcz.
Osobną sprawą są narzędzia. Szczegółowo opiszę w innym miejscu wszystkie używane w
,,barbarzyńskiej'' kuźni
narzędzia, tutaj zaś chcę wymienić tylko minimalny
zestaw, za pomocą którego taką tarczę można
wykonać:
|
KOWADŁA |
Stalowe -- | Płaskie z rogiem |
|
Drewniane -- | Dębowy pieniek |
|
MŁOTKI (typowe) |
Duży -- | 400÷500 g. |
|
Mały -- | 100÷200 g. |
|
KLESZCZE |
Płaskie |
|
Okrągłe (do prętów) |
|
GWOŹDZIOWNICA | | |
|
PILNIKI |
Płaski |
|
Półokrągły |
|
PRZECINAK |
|
PRZEBIJAK |
Okrągły |
|
NARZĘDZIA DO OBRÓBKI
DREWNA |
noże, strug, siekierka, dłuto płaskie i okrągłe,
kolce do wypalania otworów. |
|
Nie są to jakieś
wyszukane narzędzia, i znajdowały się one z pewnością w każdej ówczesnej
kuźni, a więc od strony technicznej wykonanie takiej tarczy było możliwe
właściwie w każdym, nawet najuboższym warsztacie
kowalskim.
Na zakończenie kilka obserwacji dotyczących wytrzymałości takiej osłony. Z oczywistych powodów nie przeprowadziłem prób
wytrzymałościowych kompletnej tarczy, więc wyniki moich eksperymentów
(przeprowadzonych na modelach) mogą być tylko przybliżone.
- Strzały w zasadzie nie mogły jej uczynić żadnej istotnej szkody, choć mogły
niekiedy przebić deski tarczy w pobliżu jej krawędzi.
- Tarcza mogła wytrzymać nawet silne cięcie mieczem, jeśli cios przyjęty był
płaszczyzną, natomiast uderzenie ciężkiej
spathy(2)
wyprowadzone na krawędź, nawet w poprzek słojów z pewnością zupełnie ją
niszczyło, choć cios mógł nie dosięgnąć wojownika.
- Zwykła włócznia lub oszczep wbijają się w deski lub nawet je przebijają, ale
można je wyrwać lub złamać jednym szarpnięciem bez większej szkody dla
funkcjonalności samej tarczy.
-
Pilum(3) jest chyba najgroźniejszą bronią
przełamującą tarczę, i w zasadzie była
ona wobec niego bezużyteczna. Jak wykazały próby przeprowadzone kilka
lat temu podczas Festynu Archeologicznego w Biskupinie, pilum rzucone
nawet przez przeciętnego człowieka z łatwością przebija swoim
pogrubionym ostrzem deski nawet dwa-trzy razy grubsze niż stosowane w
tarczach, leci dalej i zatrzymuje się dopiero na tulei lub drzewcu. W
praktyce pilum przebijało tarczę i nie napotykając swoim wąskim
trzpieniem oporu, mogło dosięgnąć ciała przeciwnika. Co ciekawe, sposób
przebijania pancerza jest tutaj podobny do mechanizmu działania
współczesnych podkalibrowych pocisków
przeciwpancernych.
Jak widać tarcza taka była być może
przedmiotem ,,jednorazowego użytku'', a z pewnością po każdej walce wymagała
kapitalnego remontu. Drobniejsze uszkodzenia można było co prawda naprawić
samodzielnie w warunkach ,,polowych'' (choćby łącząc przygotowanymi
wcześniej klamrami pęknięcia desek), jednak większe wymagały już
poważniejszej, fachowej naprawy. Przypuszczam, ze w większych wyprawach
brał udział i kowal, a prowizoryczną, ,,polową'' kuźnię można było
zorganizować w kilkadziesiąt minut, jednak poważne naprawy wymagały przede
wszystkim czasu, którego w takich sytuacjach mogło brakować.
1. DZIWER, (damast skuwany) - rodzaj stali o warstwowej strukturze uzyskanej poprzez wielokrotne
zgrzewanie i przekuwanie pakietu złożonego z kilku płytek o różnej zawartości węgla.
Na powierzchni wykutego z tej stali przedmiotu, widoczny jest charakterystyczny wzór.
(zobacz foto "Rekonstrukcja obosiecznego miecza rzymskiego typu GLADIUS")
(Powrót do ,,UMBO'')
2. SPATHA - długi miecz rzymski, najczęściej
wykonywany w technologii zgrzania ze sobą kilku pasm stali twardej,
miękkiej i dziweru. Głownia o długości 80 - 90 cm, waga ok. 1 kg.
(Powrót)
3. PILUM - ciężki oszczep używany w armii rzymskiej.
Jego grot miał kilkadziesiąt cm. długości i charakterystyczną długą i
cienką ,,szyję'', oraz krótkie, krępe i grube ostrze.
(Powrót)
Jesteś na stronie http://www.platnerz.com