ŻELAZO DYMARKOWE.
Stal lana, której proces produkcyjny kończy się w pierwszym etapie spustem surówki z wielkiego pieca, a w drugim odlewaniem wielotonowych kęsisk gotowej stali, jest wynalazkiem prawie nam współczesnym. Jeszcze w połowie XIX w. produkowano na skalę przemysłową wyłącznie stal zgrzewną, z wykorzystaniem procesu podlarskiego, który wynalazł w 1784 r. Henry Cont (Anglia), a pierwszą stal w postaci płynnej otrzymano dopiero po wynalezieniu konwertora bessemerowskiego do świeżenia surówki (1855 r. Henry Bessemer, Anglia). Przez prawie 3000 lat stal, a właściwie żelazo, otrzymywano w postaci ciastowatej, porowatej i zanieczyszczonej żużlem masy, którą należało oczyścić i zgrzać w jednorodna bryłę. Nie wiadomo, jak wyglądały najstarsze piece hutnicze, ani jak dokonano wynalazku otrzymywania żelaza z rudy. Temperatura zwykłego ogniska jest zbyt mała do przetopienia rudy i otrzymania łupki żelaznej, a więc najprostsza hipoteza, o przypadkowym wytopie żelaza w ognisku obłożonym nie kamieniami ale rudą żelaza, wydaje się mało prawdopodobna. Doświadczenie przeprowadzone podczas III Festynu Archeologicznego w Biskupinie (1998 r.) przez Aleksandra Strzyżewskiego i przeze mnie wykazało, że do takiego niezamierzonego wytopu mogło dojść w prostym palenisku brązowniczym. Co prawda nie udało się w wyniku tego eksperymentu uzyskać grudek kowalnego żelaza, ale wydatek cieplny i temperatura osiągnięta za pomocą prymitywnego miecha, wystarczyły do częściowego przetopienia rudy darniowej i spłynięcia żużla na dno paleniska.
Historyczne metody wytopu żelaza podzielić można (bardzo ogólnie, ze względu na postać otrzymywanego żelaza) na dwa sposoby:
- Metoda dymarska.
Uzyskiwano żelazo w postaci gąbczastej masy o ciastowatej konsystencji (łupki), wymagającej dalszego przekuwania w celu oczyszczenia z żużla i resztek węgla, oraz zgrzania w jednolitą bryłę.
Metoda stosowana w starożytności i we wczesnym średniowieczu.
- Metoda wielkopiecowa.
Żelazo otrzymywano w postaci płynnego stopu o wysokiej zawartości węgla (surówki) odwęglanej (świeżonej) następnie w procesie fryszerskim (żelazo fryszerskie) lub (po 1784 r.) pudlarskim (żelazo pudlarskie). Zaczęto ją stosować w X w. w Styrii (Austria), w XII - XIV w. rozpowszechniła się na całą Europę.
Najstarsza i najprostsza, ale budząca najwięcej kontrowersji jest metoda dymarska. Znana w całej Europie już w starożytności, w okresie wpływów rzymskich stosowana na ogromną skalę. Na terenach dzisiejszej Polski istniało wówczas kilka ośrodków produkcji żelaza - w Górach Świętokrzyskich, w okolicach dzisiejszego Opola, Warszawy i Wrocławia. Szacuje się, że w czasie swojego największego rozwoju (II - III w.n.e.) zarówno w okolicy Warszawy, jak i w Górach Świętokrzyskich produkowano przynajmniej 40 - 80 ton żelaza dymarkowego rocznie.
Na terenach dzisiejszej Polski stosowano tzw. SZYBOWE PIECE DYMARSKIE TYPU KOTLINKOWEGO. Sposób produkcji żelaza tą metodą nie jest jednak do końca odtworzony, choć znane są jego teoretyczne podstawy.
|
Rys. 1
Schemat przebiegu procesu metalurgicznego w starożytnym piecu dymarskim, według M. Radwana
|
Do naszych czasów zachowały się tylko pozostałości takich pieców hutniczych. Znajdowane na polach resztki glinianych szybów i powstałe podczas wytopu kloce żużla, o wadze przekraczającej czasem 160 kg. (Góry Świętokrzyskie oraz Pruszków, Brwinów i Milanówek k/Warszawy) a nawet 300 kg. (Tarchalice - na północ od Wrocławia), bardzo długo nie były jednoznacznie wiązane ze starożytną działalnością hutniczą. Dopiero badania archeologiczne prowadzone od 1955 r. w okolicach Nowej Słupi (Góry Świętokrzyskie) przez Kazimierza Bielenina, ówczesnego kustosza Muzeum Archeologicznego w Krakowie, przy współpracy Mieczysława Radwana, wówczas docenta Akademii Górniczej w Krakowie, pozwoliły na próbę rekonstrukcji takiego pieca. Badania doświadczalne nad jego odtworzeniem rozpoczął prof. M. Radwan w 1957 r. W laboratorium AGH w Krakowie, a następnie na terenie Starachowickich Zakładów Budowy Samochodów.
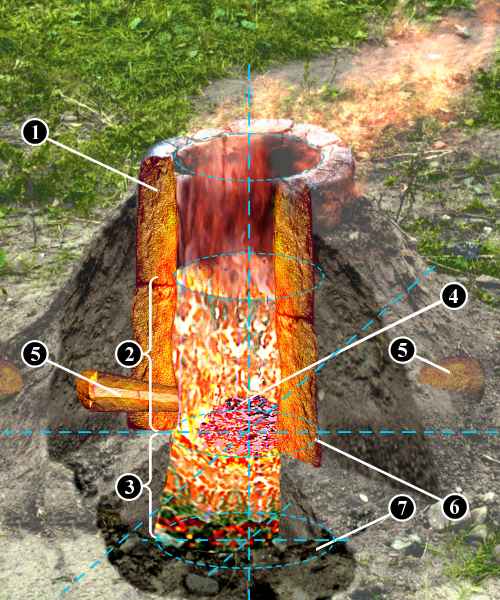 |
|
Rys. 2
Budowa doświadczalnego dymarskiego pieca szybowego typu kotlinkowego, z dmuchem sztucznym.
(konstrukcja autora)
|
1 - Szyb pieca. 2 - Wsad (węgiel drzewny + ruda żelaza). 3 - Kotlinka wypełniona ściekającym podczas wytopu żużlem. 4 - łupka żelaza. 5 - Dysze. 6 - Pierwotny poziom terenu. 7 - Poziom dna kotlinki.
|
Typowy dymarski piec szybowy typu kotlinkowego z początków naszej ery (bardzo często mylony z DYMARKĄ, a więc piecem średniowiecznym) miał bardzo prostą budowę. W ziemi wykopywano kotlinkę o ścianach cylindrycznych lub lekko stożkowatych, o głębokości 30-80 cm. i średnicy 25-60 cm. Nad tym dołkiem budowano z gliny szyb o przypuszczalnej wysokości od 50 do 150 cm. W dolnej części szybu wykonywano kilka otworów dmuchowych, do których być może podłączone były dysze tłoczące powietrze z miechów. Możliwe, że szyb obsypywano warstwą ziemi w celu uzyskania wyższej temperatury wewnątrz pieca (dodatkowa izolacja termiczna). Kotlinkę następnie wypełniano grubym węglem drzewnym lub dokładnie wysuszonymi, ustawionymi pionowo szczapami drewna. Na utworzony w ten sposób ruszt wsypywano rozżarzony węgiel drzewny i stopniowo rozgrzewano cały piec. Po rozgrzaniu pieca, do jego wnętrza wsypywano porcje węgla drzewnego i rudy żelaza, tak utrzymując wysokość wsadu i ilość węgla i rudy, aby temperatura żaru na wysokości dysz utrzymywała się w granicach 1400°C (kolor białego-niebieskawego żaru). W wysokich temperaturach i w obecności nadmiaru węgla i tlenku węgla, następował proces redukcji rudy do metalicznego żelaza. Nie otrzymywano jednak ciekłego metalu jak obecnie, lecz zawiesinę mikroskopijnych kuleczek żelaza w ciekłym żużlu. W miarę spływania tej masy w rejon najwyższych temperatur (poziom dysz), następowało częściowe spieczenie kuleczek żelaza w rodzaj metalowej błonki otaczającej kawałki węgla drzewnego. Powstawała więc jakby metalowa gąbka lub piana, składająca się z takich "pęcherzy", pomieszanych z węgłem drzewnym i resztkami niezredukowanej rudy, oraz oblewającego tę "pianę" i wypełniającego jej wolne przestrzenie ciekłego żużla. Po kilkunastu godzinach pracy pieca dosypywano już tylko sam węgiel, aby ostatecznie wytopić resztę żużla z otrzymanej w ten sposób "gąbki", i spiec pozostałe w nim drobinki metalu w większe bryłki. Kiedy na dnie pieca pozostała już tylko gąbczasta masa - ŁUPKA - i wypalił się prawie cały węgiel drzewny, rozbijano nadziemną część pieca (gliniany szyb) i odklejano łupkę od płynnego żużla wypełniającego część podziemną - KOTLINKĘ.
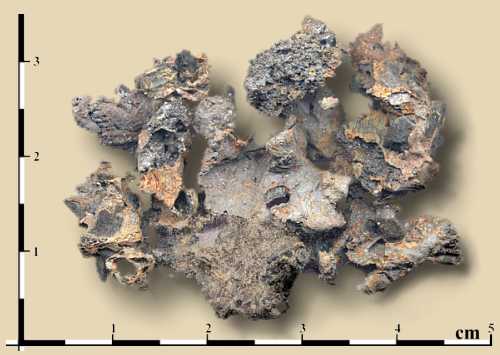 |
|
Rys. 3
Fragment łupki żelaznej uzyskanej w doświadczalnym piecu dymarskim.
|
Na tym kończono sam wytop, na tym kończyła się też rola właśnie rozbitego pieca. Do kolejnego wytopu budowano obok następny piec, a po poprzednim pozostawała w ziemi zalana żużlem kotlinka i resztki rozbitego szybu. Otrzymana w takim piecu łupka podlegała dalszej obróbce. Należało ją ponownie rozgrzać do temperatury białego żaru i obkuwając drewnianymi (?) młotami usunąć z jej porów nadmiar żużla i resztę węgla drzewnego.
 |
|
Rys. 4
Szlif fragmentu łupki żelaznej.
1 - Żużel
2 - Przecięty pęcherz spieczonego żelaza.
3 - Węgiel drzewny.
|
Końcowe etapy tej operacji przeprowadzano żelaznymi młotkami na metalowym lub kamiennym kowadle, gdyż należało teraz zgrzać porowatą bryłę w całość, przy czym następowało również częściowe nawęglenie żelaza. Jest mało prawdopodobne, aby z każdego wytopu otrzymywano jeden duży kęs metalu o wadze kilku-kilkunastu kg. Przypuszczalnie było to wiele mniejszych fragmentów o prostokątnym lub wrzecionowym kształcie i wadze kilkuset gram, a więc zupełnie wystarczające do wykonania większości używanych wówczas przedmiotów żelaznych.
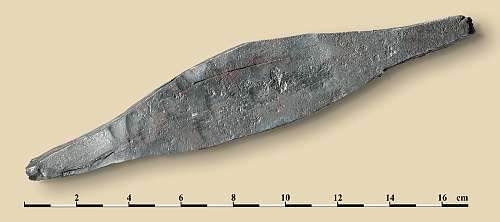 |
|
Rys. 5
Kęs żelaza dymarkowego powstały ze zgrzania łupki (rekonstrukcja).
|
Dymarska metoda produkcji żelaza, tylko z pozoru była prymitywna. Z pewnością była bardzo pracochłonna i mało wydajna, gdyż zawartości tlenków żelaza w żużlu dochodzi do 50%, a więc uzysk czystego żelaza z rudy był niewielki. Trudno było też kontrolować skład otrzymywanego metalu ze względu na jego ciastowatą a nie płynną konsystencję. Nie znaczy to jednak, że nie można było otrzymać w ten sposób żelaza o doskonałych parametrach. Dawni kowale bardzo dobrze potrafili regulować jakość metalu, choć wymagało to dużego doświadczenia, a często ogromnego nakładu pracy i czasu. Metodą wielokrotnego przekuwania i ponownego zgrzewania żelaza dymarkowego, można było zarówno wyrównać jego skład chemiczny, jak i nawęglić, a więc utwardzić, lub przeciwnie - odwęglić, a więc zmiękczyć metal. Poprzez wygrzewanie w węglu drzewnym można selektywnie nawęglić tylko powierzchniowe warstwy wyrobu, a więc na miękkim, ciągliwym rdzeniu utworzyć twardą warstwę poddającą się hartowaniu. Wielokrotne przekuwanie i zgrzewanie nadaje metalowi jeszcze jedną bardzo cenną zaletę - strukturę pasmowatą. Stal współczesna, produkowana w postaci ciekłej, tzw. stal zlewna, tylko z pozoru ma jednolitą budowę. W rzeczywistości ma ona strukturę ziarnistą, utworzoną z zespolonych ze sobą kryształów metalu o wielkości rzędu 0,005 - 1 mm.
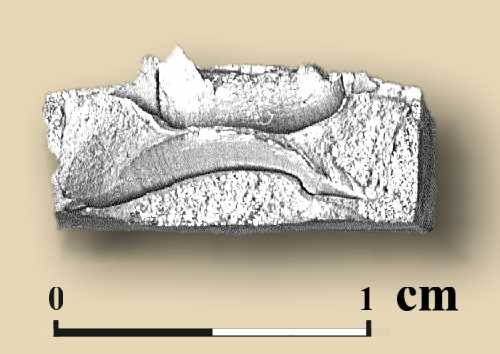 |
|
Rys. 6
Ziarnista struktura stali na przełomie trzpienia głowni kutej warstwowo.
|
Każda wada materiału (pęcherze gazu, zgorzelina, zanieczyszczenia itp.) powoduje osłabienie materiału w tym miejscu. Dlatego ewentualne pęknięcie powstałe na skutek silnego uderzenia powstanie najprawdopodobniej właśnie tam, gdzie taka wada materiału się znajduje, a linia tego pęknięcia pobiegnie po granicy spojonych ze sobą kryształów stali. Zelazo dymarkowe powstawało w wyniku zgrzewania łupki żelaznej (stal zgrzewna), a więc z małych, zgrzewanych ze sobą kawałków metalu. Powierzchnia tych pierwotnych kawałków żelaza odwęgliła się w trakcie zgrzewania ponadto pozostały na niej liczne zanieczyszczenia, resztki żużla itp., które w wyniku wyciągania, ponownego zgrzewania i znowu wyciągania nadawały całej bryle strukturę włóknistą. Kryształy metalu nie stanowiły już jednej zwartej masy, lecz tworzyły wiązki włókien. Ewentualne pęknięcie jednego włókna nie może przenieść się tak łatwo na sąsiednie, lecz zostaje przerwane na jego granicy, a wtrącenia żużla i inne zanieczyszczenia układające się pomiędzy włóknami metalu dodatkowo w takim przerwaniu linii pęknięcia pomagają. Bardzo podobną budowę mają znane powszechnie laminaty z włókien szklanych czy węglowych, a nawet klejone szyby samochodowe. Taka struktura wybitnie zmniejsza wrażliwość stali i żelaza na gwałtowne uderzenia skierowane w poprzek włókien, zmniejsza też niestety ich ogólną twardość. Miecz wykuty z wielokrotnie przekuwanego i zgrzewanego żelaza, jest więc o wiele bardziej odporny na uderzenia i złamanie od miecza wykutego z jednorodnej stali. Chyba najlepszym dowodem na możliwość uzyskania doskonałej jakości żelaza dymarkowego jest fakt, że choć w minimalnych ilościach, jednak produkuje się takie żelazo do dziś, a jego cena osiąga zawrotne sumy. Właśnie tą metodą uzyskuje się metal do wyrobu najlepszych egzemplarzy mieczów japońskich, a łupki żelaza dymarkowego (tomahagane) objęte są zakazem wywozu poza granice Japonii.
Pomimo licznych analogii, japońska metoda produkcji żelaza dymarkowego różni się w istotny sposób od metody stosowanej na Mazowszu czy w Górach Świętokrzyskich. Nie znamy co prawda szczegółów metod starożytnych, gdyż jak dotąd nikomu nie udało się jej w pełni, w wiarygodny sposób zrekonstruować, znane są jednak jej kluczowe cechy. Przede wszystkim łupka żelazna uzyskana na naszych terenach wydobywana była z pieca na gorąco, kiedy żużel w kotlince był jeszcze płynny. Dowodzą tego ślady narzędzi, mogące powstać tylko podczas odklejania łupki od jeszcze miękkiej a więc rozżarzonej powierzchni kloca. Również sama łupka obtapiana była z resztek żużla na gorąco i od razu zgrzewana w całość, o czym świadczą tzw. żużle miseczkowate, bryłki żużla zastygające na dnie bardzo silnie rozpalonego paleniska kowalskiego. Natomiast metoda stosowana w Japonii polega na rozbiciu zimnej łupki. Wybierane drobne okruchy metalu (grąpie) układano na płytce żelaznej, którą następnie zawijano i zgrzewano w jedną całość. Tak uzyskana sztabka znów była rozkuwana na płytkę, znów dodawano następną porcję wybranych z rozbitej łupki grąpi, i znów zgrzewano. Za każdym razem masa płytki powiększała się o nowe, zgrzane z nią kawałki metalu.
Jesteś na stronie http://www.platnerz.com